Blow Mold Processes
Blow molding is a manufacturing process for the production of commercial plastic bottles. This page is intended to give a brief summary of each blow molding process and the respective bottle forming capability.
Click the links below to learn more about each type of blow molding process:
To learn more about the forming capabilities of each process click here.
Extrusion blow molding (EBM)
Extrusion blow molding starts with plastic pellets fed through to reciprocating screw where they are enclosed by a barrel. The barrel has heating elements that will melt the pellets. The molten polymer will be extruded to form a hollow tube, referred to as the parison. The parison will be encased by the mold and subsequently blown into the mold cavity forming the final bottle shape.
Containers can be made in a wide range of sizes, shapes, neck finishes. Containers can be formed with or without handles.
General applications of EBM containers are found within Health & Beauty, Automotive, Nutraceutical/Pharmaceutical, Pet Care, Laundry, Home Care Products, Industrial and Household Chemicals.
Injection Stretch Blow Molding (ISBM)
ISBM process allows the material to stretch in a vertical and a horizontal manner simultaneously creating bi-axle orientation of the molecules. This allows for the bottle to be made at lighter weights while maintaining its overall strength and part integrity and providing glass like clarity. Bottles are primarily made with PET resins but in certain applications, the use of PP has shown outstanding results, both in a wide range of shapes and sizes.
General applications of ISBM containers are found within Health & Beauty, carbonated & non-carbonated Beverages, Water, home care products, cleaners, spices, sauces, jams, cooking oils dressings, liquor and certain Pharma applications.
Injection stretch blow molding can be further categorized between 1-Stage or 2-Stage injection stretch blow molding. Both stages necessitate a preform to be blown. A preform will have the desired thread dimensions of the bottle but will need to be blown to the final bottle shape. The injection stretch process uses high pressure air and a rod to stretch out the preform. The rod will stretch out the preform just before being blown. The addition of the stretch rod allowed for bigger bottles and intricate designs as the preform is distributed and stretched out just before being blown to shape. The main difference between a 1 or 2 stage operation is the preform treating.
1 Stage Stretch Blow Molding
In a 1 stage operation, the process begins with the production of the preform. A molten polymer is injected into a die to create the preform. The preform will subsequently travel to the blowing station where it will enter a mold and be blown to the final bottle shape. The entire bottle production process is completed in a single stage.
2 Stage Stretch Blow Molding
For a 2 stage operation, as the name suggests, the bottles are formed in two stages. The initial stage is where the preform is manufactured. The final stage occurs at a different machine where the preform is blown to the final bottle shape.
Injection Blow Molding (IBM)
Injection blow molding occurs within a single stage process. A preform is manufactured via injection molding and is subsequently transferred to a blowing station where it will be blown to its final bottle shape. The preform’s thread will be the thread finish on the bottle.
The main difference between injection and injection stretch blow molding lies within the blow molding process. The injection blow molding machine uses high pressure air to blow out the preform to the mold cavity shape. The injection stretch process uses high pressure air and a stretch rod. The stretch rod will stretch out the preform to the bottle size exactly before being blown. The addition of the stretch rod allowed for bigger bottles and intricate designs as the preform is distributed and stretched out just before being blown to shape.
IBM is often used to manufacture products that require neck finishes with high tolerance requirements and for applications using ‘plug’ type caps. This process is also well suited for high volume outputs. This process allows for bottles to be made that has no flash therefore allowing a high end ‘clean’ finish.
General applications of IBM containers are ideal for personal care, OTC Pharmaceutical and fragrance based products.
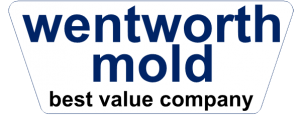
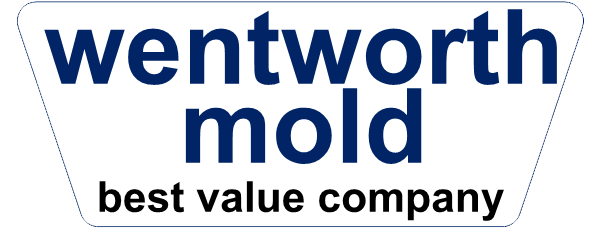